1、問題描述
由于市場需求的變化,1500 型搓齒機產能嚴重不足,而 1000 型搓齒機產能過剩,出現了兩種機型產能不均衡的問題。為了解決這一產能不均衡的問題,希望通過提高 1000 型搓齒機利用率,緩解或解決 1500 型搓齒機產能壓力,且避免新增設備投入。
2、1000 型和 1500 型搓齒機工藝參數分析
搓齒最大模數、搓齒最大外徑、搓齒最大寬度、最大工件長度、搓齒板安裝最大寬度、開口部尺寸均可以根據被加工產品外形尺寸和花鍵參數直接選擇。由于搓齒圈數決定了搓齒板長度,而搓齒圈數與被加工工件壓力角有關,因此只有確定搓齒圈數后才能確定可安裝搓齒板規(guī)格和滑鞍最大行程。1000 型和 1500 型搓齒機主要工藝參數詳見表 1。
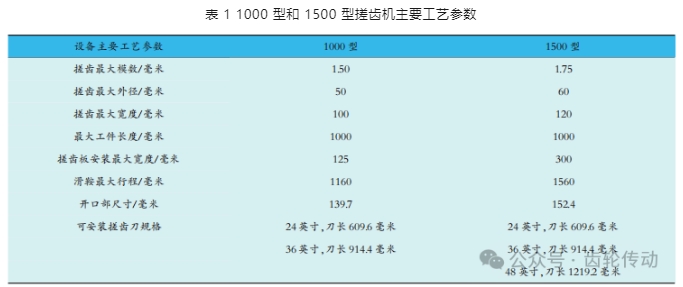
3、搓齒板圈數的選擇
通常加工 30°壓力角的花鍵需要搓 8 圈以上,加工 37.5°壓力角的花鍵需要搓 7 圈以上,加工 45°壓力角的花鍵需要搓 6 圈以上。搓齒圈數越多齒升量就越小,搓齒圈數越少齒升量就越大。搓齒板齒升量過大,易造成搓齒板損傷、加工機床負載過大而振動、工件齒距累積不合格。搓齒板齒升量過小,則搓齒板長度較長,搓齒加工時間長,需要較大滑鞍行程的設備,且刀具采購成本高。
搓齒板齒升量設計一般不大于 0.003 毫米,齒升量的計算主要與被加工工件的花鍵大徑、花鍵小徑、刀具齒數設計有關,設備選型時搓齒板齒升量可運用公式(1)—(3)進行計算。

式中:fz 為搓齒板齒升量,D 為被加工工件花鍵大徑,d 為被加工工件花鍵小徑,Z 為搓齒板刀具齒數,z 為被加工工件花鍵齒數,Mn 為被加工工件花鍵模數,N 為搓齒板圈數,t 為搓齒板齒距。
4、1500 型搓齒機加工產品齒升量再計算
運用公式(1)—(3)對 1500 型搓齒機加工產品的齒升量進行計算,尋找可轉移至 1000 型設備上加工的產品,以此解決 1500 型搓齒機產能不足的問題。計算結果見表 2。
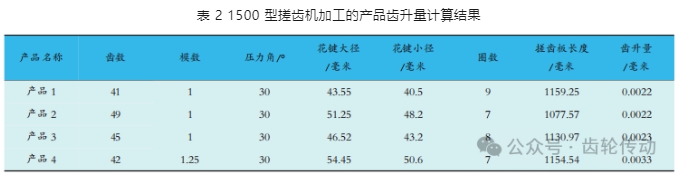
通過對 1000 型和 1500 型搓齒機產能計算,產品1、產品 2、產品 3 的齒升量均小于 0.003 毫米。其中產品 1 需求量較大,若產品 1 能夠實現在 1000 型搓齒機加工,即可解決 1500 型搓齒機產能不足的問題,兩種設備利用率接近平衡。
5、改進與驗證
由表 2 可知,產品 2 和產品 4 花鍵壓力角雖然也都是 30°,但搓齒圈數僅 7 圈,較上述搓齒板應選擇圈數 8 圈少 1 圈。因此,搓齒圈數并不是必須嚴格按照 30°壓力角 8 圈、37.5°壓力角 7 圈、45°壓力角 6 圈對應選擇。
對產品 1 搓齒圈數減少至 7 圈進行計算,得到齒升量為 0.0028 毫米、刀具長度為 901.64 毫米,即刀具齒升量小于 0.003 毫米、刀具長度小于 36 英寸。為保障產品 1 在 1000 型搓齒機上加工的可行性,經與刀具廠家確認,1000 型搓齒機可以滿足產品 1 的加工要求,搓齒板刀具長度為 36 英寸、914 毫米。
對改進后的搓齒板進行符合性和穩(wěn)定性加工驗證,連續(xù)加工 50 件,齒輪檢測中心檢測其花鍵精度均合格,花鍵精度可穩(wěn)定達到《圓柱直齒漸開線花鍵(米制模數 齒側配合)第 1 部分:總論》(GB/T 3478.1— 2008)中規(guī)定的 6 級(以下簡稱 GB/T 3478.1 6 級)。搓齒板連續(xù)使用 3 個月,加工數量已達 2 萬件,搓齒板目視沒有明顯損傷,加工過程中機床也沒有出現明顯振動現象。此外,改進后的搓齒板長度為 36 英寸,1000 型搓齒機和 1500 型搓齒機均可以安裝,搓齒板實現了兩種機型的通用。改進后搓齒板長度減少 305 毫米,加工效率提升約 1.5 秒 / 件。
為進一步驗證以齒升量大小選擇設備機型方法的有效性,對表 2 中產品 2 和產品 3 能否在 1000 型搓齒機上加工進行可行性計算分析。產品 2 外徑為 51.25 毫米,超出了 1000 型搓齒機搓齒最大外徑 50 毫米的范圍,故不可行。產品 3 按照搓 6 圈計算,搓齒板長度約為 848 毫米,刀具齒升量為 0.0031 毫米,分析結果可行。同樣,對改進后搓齒板進行符合性和穩(wěn)定性加工驗證,驗證結果顯示花鍵精度可穩(wěn)定達到 GB/T 3478.1 6 級,搓齒板目視沒有明顯損傷,加工過程機床相對平穩(wěn)。
6、結語
通過齒升量選擇搓齒機機型的方法,實現了產品 1 和產品 3 在 1000 型搓齒機和 1500 型搓齒機互換加工,不僅解決了 1500 型搓齒機產能不足的問題,還提高了產品 1 的加工節(jié)拍。此外,本方法還在一定程度上規(guī)避了大批量生產過程中出現設備故障而導致停線的風險。